BATTERY MONITORING SYSTEMS
The efficiency of the batteries is the first condition for the reliability of UPS (uninterruptible power systems) and for Rectifiers. Statistically, over the 50% of the failures of these equipment are due to defective batteries.
For this reason the batteries require continuous monitoring and periodic test.
BMS Sentry – Battery Monitoring System
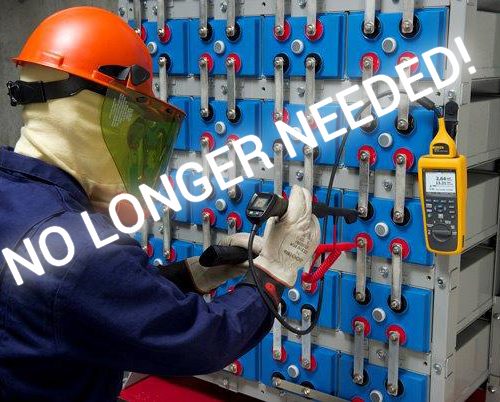
BMS-Sentry monitors a battery by continuously processing and storing the operating parameters of each monoblock and in particular the values of voltage, internal resistance, temperature and ripple. Providing a timely analysis, it is able to capture the first real moments of degradation of one or more monoblocks, allowing you to promptly replace a battery when the very first signs of degradation begin to appear. BMS-Sentry also detects charging system failures which can quickly damage the batteries.
BMS-SENTRY therefore avoids the damages that an inefficient battery would produce in presence of power outages. It avoid the cost of a new battery when the old one could still be efficient for one or more years. So it allows you to decide a replacement based on certain data and not on the basis of infrequent tests and life time declared by the battery manufacturers.
BMS-SENTRY can be used both in the fixed version, dedicated to the continuous monitoring of a series of monoblocks, and in the portable version to monitor more batteries.
BMS-SENTRY is compatible with VRLA sealed batteries, stationary and Ni-Cd batteries.
The BMS-Sentry module is a complete instrument that can detect all the cases that make a battery unreliable.
In cases where the accumulators have to sustain significant discharge regimes (high currents compared to their limits) it is advisable to carry out a discharge test annually, to verify their integrity from the point of view of electrochemical resistance, a parameter that is not always identifiable in a predictive way.
However, tests done with discharger devices only have many disadvantages.
First of all, the battery discharge curves, provided by the dischargers in use, highlight the total V, an absolutely misleading value to determine the battery reliability. It is essential to know the voltage level of each monoblock, a measure provided by the BMS-Sentry. For this reason only, discharge tests require the joint use of BMS modules.
In addition, during the tests, the maintenance workers have to section the battery, to access inside the cabinets, in presence of dangerous voltages, to connect the discharge device and, always with the batteries live, they have to proceed manually with the measurements on the monoblocks by removing the terminal protections and working in narrow spaces, all this with obvious risks for workers safety. Furthermore, it will take several minutes to record the measurements from the first to the last monoblock. Therefore comparable measurements taken at the same time will not be available, as with the use of BMS.
Sectioning the battery is a further problem as there will be no load protection if a black-out occurs during the test.
The solution is the use of DMU – Discharge Management Unit (patented). This device allows the operators to work in complete safety, without access to the battery cabinets, by directly connecting the batteries to the dischargers and, at the same time, protecting the loads in case of a main failure. In fact, in the event of a black-out the test is stopped, but the batteries, in zero time, become available to the real loads. In order to perform a battery discharge test it will no longer be necessary to wait for a plant stop, or install emergency UPS and rectifiers or temporarily set up additional batteries.
DMU is an innovative, standardized device, with an absolutely low cost, the utility of which already makes it absolutely necessary today.
In short: BMS, providing a continuous monitoring, and DMU for battery discharge test, offers togheter the best results, without risks exposure, managing and storing all test parameters.
– They provide reports with accurate and intuitive data for an optimal interpretation of the results;
– They make it easier and faster to perform battery tests
– They allow to operate in complete safety of the staff, overcoming the risks currently present during the execution of these controls.
BMS-Sentry and DMU therefore allow rapid controls on the reliability and efficiency of the batteries based on certain data, avoid work with safety risks and reduce the battery maintenance to the few seconds needed to start a device that replace the many work hours of a maintenance technician.
There are many BMS models available, those most often used are:
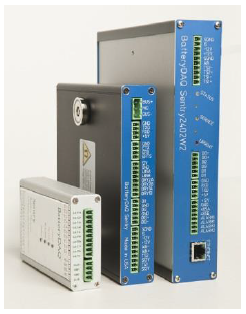
BMS Sentry 4412 for testing up to 44 12V battery monoblocks
BMS Sentry 2412 for testing up to 24 12V monoblocks
BMS Sentry 1012 for testing up to 10 12V monoblocks or 20 6V monoblocks
BMS Sentry 1202 e 2402 for testing up to 12 or 24 2V monoblocks
BMS Sentry 6002 for testing up to 60 2V monoblocks
This is a short presentation; contact us for further information or to identify the best solution for the maintenance of your batteries. We are then available, upon your request, to present the operating characteristics and usefulness of these products and of the DMUs ‘in the field’, at our headquarters in Trezzano sul Naviglio, Milan, Italy.